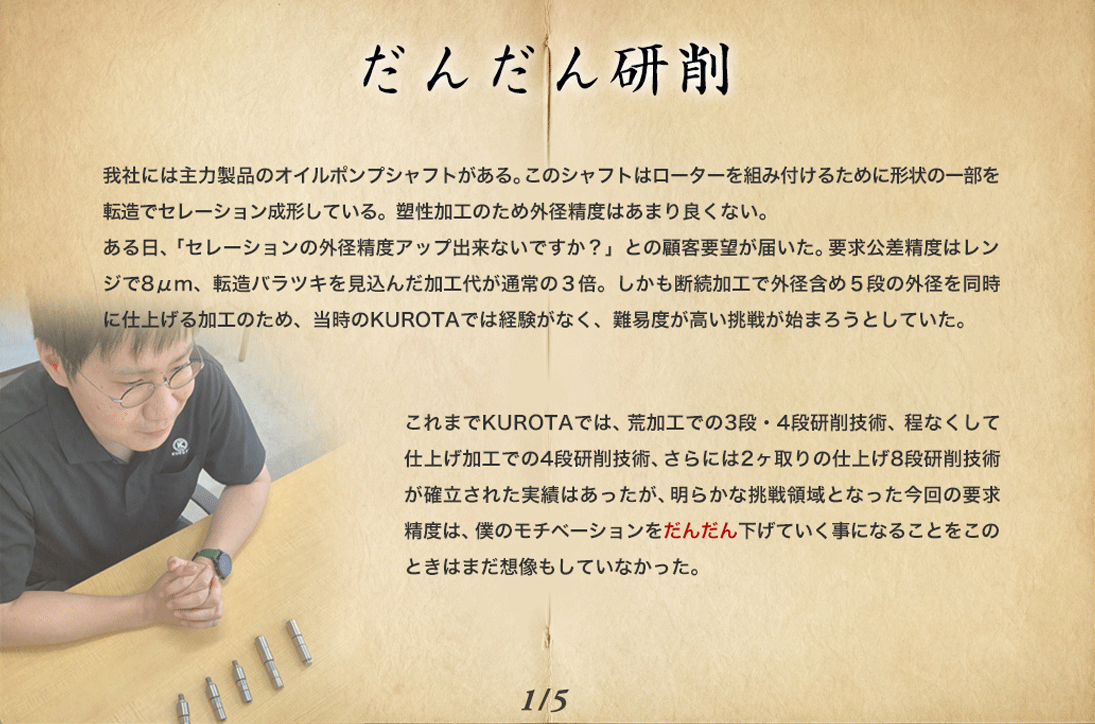
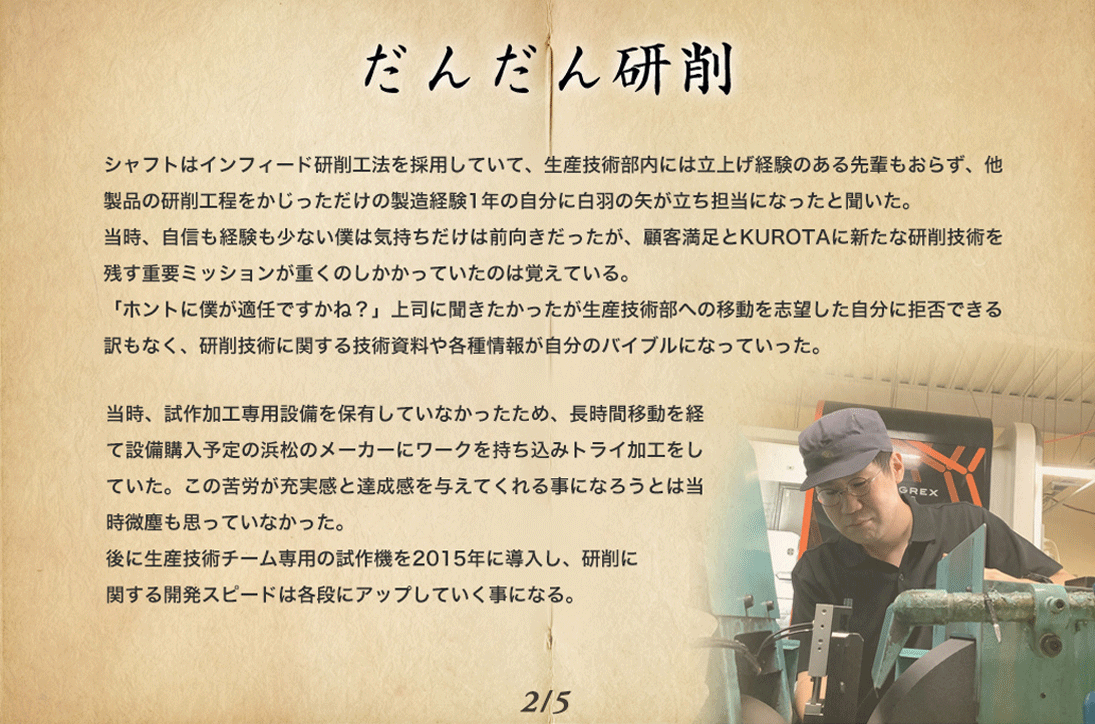
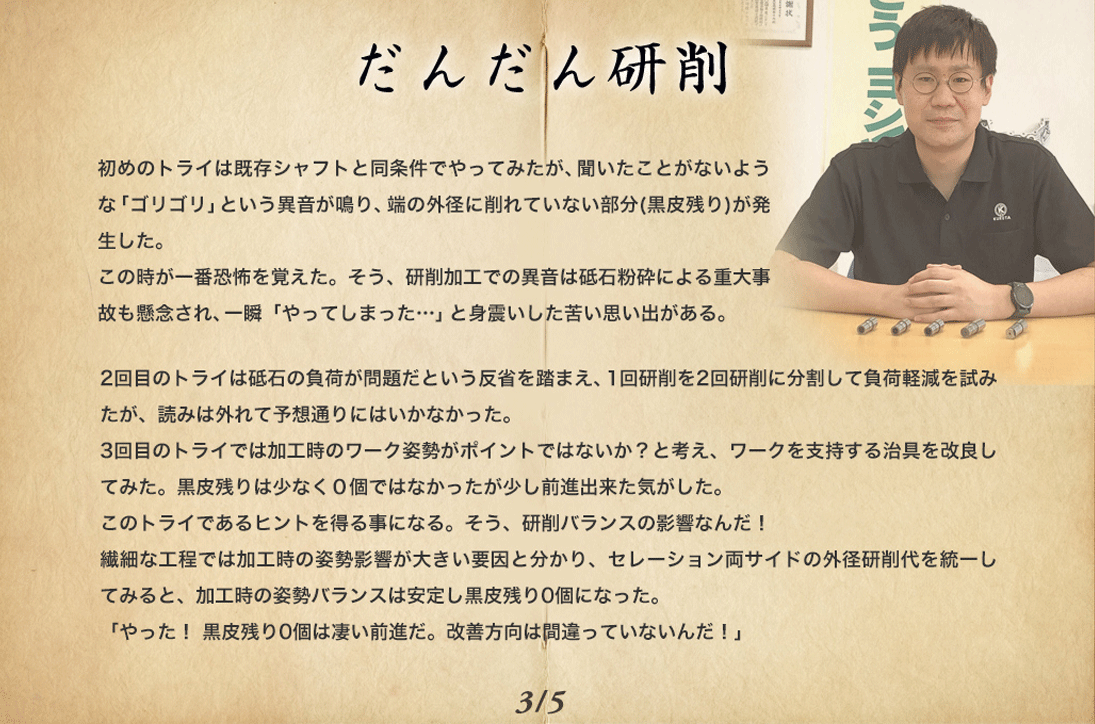
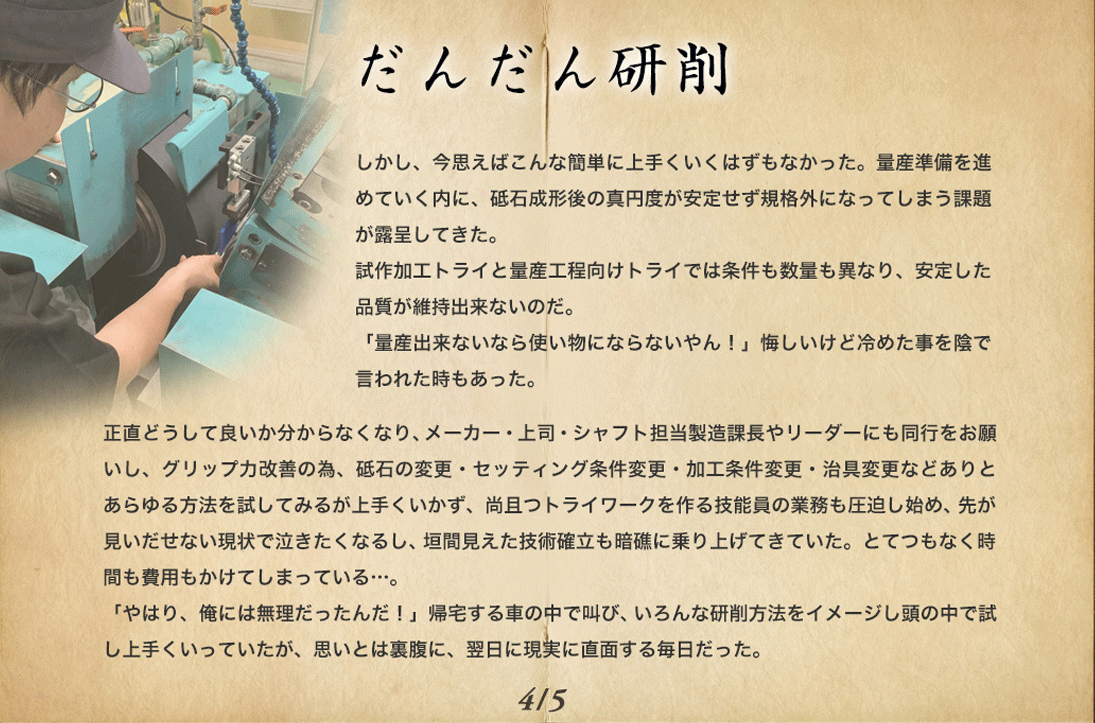
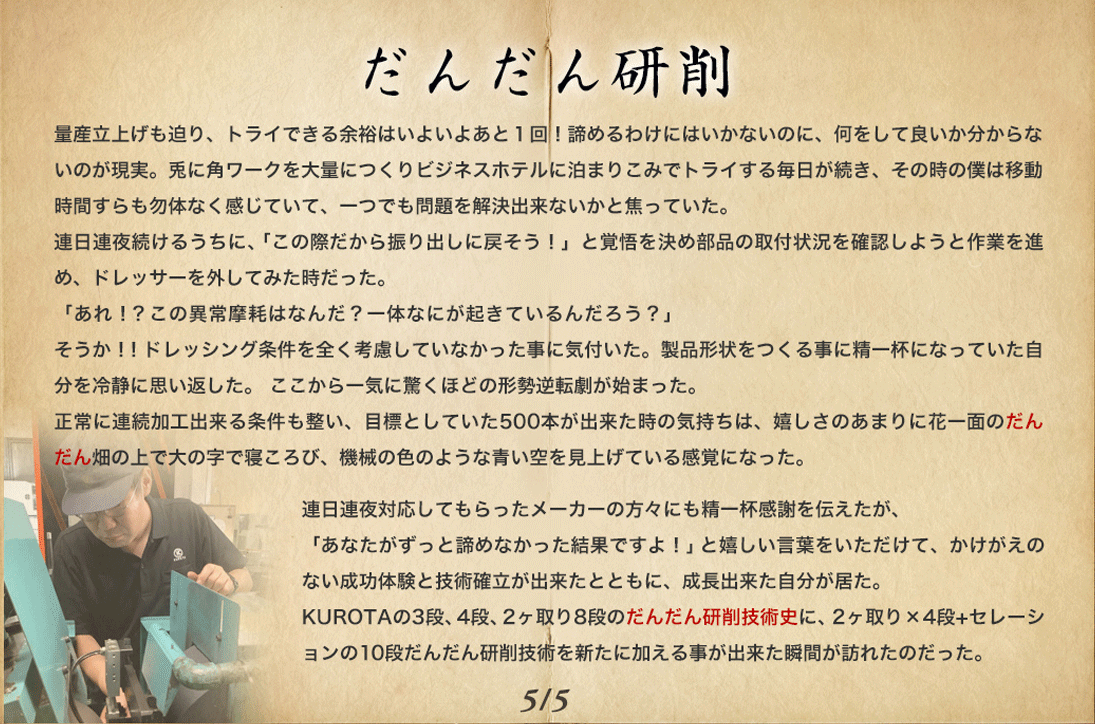
だんだん研削
我社には主力製品のオイルポンプシャフトがある。このシャフトはローターを組み付けるために形状の一部を転造でセレーション成形している。塑性加工のため外径精度はあまり良くない。
ある日、「セレーションの外径精度アップ出来ないですか?」との顧客要望が届いた。要求公差精度はレンジで8μm、転造バラツキを見込んだ加工代が通常の3倍。しかも断続加工で外径含め5段の外径を同時に仕上げる加工のため、当時のKUROTAでは経験がなく、難易度が高い挑戦が始まろうとしていた。
これまでKUROTAでは、荒加工での3段・4段研削技術、程なくして仕上げ加工での4段研削技術、さらには2ヶ取りの仕上げ8段研削技術が確立された実績はあったが、明らかな挑戦領域となった今回の要求精度は、僕のモチベーションをだんだん下げていく事になることをこのときはまだ想像もしていなかった。
1/5
だんだん研削
シャフトはインフィード研削工法を採用していて、生産技術部内には立上げ経験のある
先輩もおらず、他製品の研削工程をかじっただけの製造経験1年の自分に白羽の矢が立ち担当になったと聞いた。
当時、自信も経験も少ない僕は気持ちだけは前向きだったが、顧客満足とKUROTAに新たな研削技術を残す重要ミッションが重くのしかかっていたのは覚えている。
「ホントに僕が適任ですかね?」上司に聞きたかったが生産技術部への移動を志望した自分に拒否できる訳もなく、研削技術に関する技術資料や各種情報が自分のバイブルになっていった。
当時、試作加工専用設備を保有していなかったため、長時間移動を経て設備購入予定の浜松のメーカーにワークを持ち込みトライ加工をしていた。この苦労が充実感と達成感を与えてくれる事になろうとは当時微塵も思っていなかった。
後に生産技術チーム専用の試作機を2015年に導入し、研削に関する開発スピードは各段にアップしていく事になる。
2/5
だんだん研削
初めのトライは既存シャフトと同条件でやってみたが、聞いたことがないような「ゴリゴリ」という異音が鳴り、端の外径に削れていない部分(黒皮残り)が発生した。
この時が一番恐怖を覚えた。そう、研削加工での異音は砥石粉砕による重大事故も懸念され、一瞬「やってしまった…」と身震いした苦い思い出がある。
2回目のトライは砥石の負荷が問題だという反省を踏まえ、1回研削を2回研削に分割して負荷軽減を試みたが読みは外れて予想通りにはいかなかった。
3回目のトライでは加工時のワーク姿勢がポイントではないか?と考え、ワークを支持する治具を改良してみた。黒皮りは少なく0個ではなかったが少し前進出来た気がした。
このトライであるヒントを得る事になる。そう、研削バランスの影響なんだ!繊細な工程では加工時の姿勢影響が大きい要因と分かり、セレーション両サイドの外径研削代を統一してみると、加工時の姿勢バランスは安定し黒皮残り0個になった。
「やった! 黒皮残り0個は凄い前進だ。改善方向は間違っていないんだ!」
3/5
だんだん研削
しかし、今思えばこんな簡単に上手くいくはずもなかった。量産準備を進めていく内に、砥石成形後の真円度が安定せず規格外になってしまう課題が露呈してきた。
試作加工トライと量産工程向けトライでは条件も数量も異なり、安定した品質が維持出来ないのだ。
「量産出来ないなら使い物にならないやん!」悔しいけど冷めた事を陰で言われた時もあった。
正直どうして良いか分からなくなり、メーカー・上司・シャフト担当製造課長やリーダーにも同行をお願いし、グリップ力改善の為、砥石の変更・セッティング条件変更・加工条件変更・治具変更などありとあらゆる方法を試してみるが上手くいかず、尚且つトライワークを作る技能員の業務も圧迫し始め、先が見いだせない現状で泣きたくなるし、垣間見えた技術確立も暗礁に乗り上げてきていた。とてつもなく時間も費用もかけてしまっている…。
「やはり、俺には無理だったんだ!」帰宅する車の中で叫び、いろんな研削方法をイメージし頭の中で試し上手くいっていたが、思いとは裏腹に、翌日に現実に直面する毎日だった。
4/5
だんだん研削
量産立上げも迫り、トライできる余裕はいよいよあと1回!諦めるわけにはいかないのに、何をして良いか分からないのが現実。兎に角ワークを大量につくりビジネスホテルに泊まりこみでトライする毎日が続き、その時の僕は移動時間すらも勿体なく感じていて、一つでも問題を解決出来ないかと焦っていた。
連日連夜続けるうちに、「この際だから振り出しに戻そう!」と覚悟を決め部品の取付状況を確認しようと作業を進め、ドレッサーを外してみた時だった。
「あれ!?この異常摩耗はなんだ?一体なにが起きているんだろう?」
そうか!!ドレッシング条件を全く考慮していなかった事に気付いた。製品形状をつくる事に精一杯になっていた自分を冷静に思い返した。 ここから一気に驚くほどの形勢逆転劇が始まった。
正常に連続加工出来る条件も整い、目標としていた500本が出来た時の気持ちは、嬉しさのあまりに花一面のだんだん畑の上で大の字で寝ころび、機械の色のような青い空を見上げている感覚になった。
連日連夜対応してもらったメーカーの方々にも精一杯感謝を伝えたが、「あなたがずっと諦めなかった結果ですよ!」と嬉しい言葉をいただけて、かけがえのない成功体験と技術確立が出来たとともに、成長出来た自分が居た。
KUROTAの3段、4段、2ヶ取り8段のだんだん研削技術史に、2ケ取り×4段+セレーションの10段だんだん研削技術を新たに加える事が出来た瞬間が訪れたのだった。』
5/5